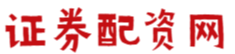
发布日期:2024-11-09 21:58 点击次数:120
继年初工信部等五部门联合印发《关于开展智能网联汽车“车路云一体化”应用试点的通知》(以下简称《通知》)之后,7月3日,五部门正式公布我国将在北京、上海、广州、深圳、重庆、沈阳等20个城市开展智能网联汽车“车路云一体化”应用试点,这标志着我国智能网联汽车产业化进程又迈出实质性一步。
值得注意的是,交易公告中提到MLF操作采用了利率招标方式,即参与机构在投标时可以选择多个利率,最终的中标结果也更能反映资金供需状况。从实际效果看,本次MLF利率适度下行,较好地弥合了与同业存单等市场利率的差异。
RO反渗透膜系统的清洗与消毒
1. 序 言
RO反渗透膜技术近些年来发展起来的先进膜分离(FILMSEP: FILM SEPERATION;MEMSEP:MEMBRANE SEPERATION),和膜技术(FILMTEC: FILM TECHNOLOGY),已经成为很多行业的优选的水处理技术方案,正成为水处理行业内主打水处理工艺技术。
水处理系统进水中存在各种形式可导致反渗透和纳滤膜表面污染的物质,例如水合金属氧化物、含钙沉淀物、有机物及生物。污垢(fouling)就是指覆盖在膜表面上的各种沉积物,包括水中的结垢物。
膜系统预处理的目的在于尽量减少膜表面的上述污染,通过安装合适的预处理系统,选择恰当的操作条件,如产水流量,运行压力与产水回收率等,就能达到这一目标。
下列因素有可能引起膜系统污垢:
预处理系统不完善
预处理运行不正常
系统选材不合适(泵和管线等)
预处理投药系统失灵
系统停机后冲洗不及时或不充分
操作控制不当
膜面长时间累积沉淀物(钡和硅垢等)
进水组份或其它条件改变
进水受生物污染
发生膜表面的污垢将加速系统性能的下降,如减少产水流量,降低脱盐率。污垢的另一个负面现象是进水和浓水间的压差增加。
由于进口品牌的RO膜及膜元件具有全球膜工业界能承受最宽的pH和温度条件,只要措施得力及时,就可以很有效地进行系统清洗,最大限度地恢复膜系统的性能。但若拖延太久才进行清洗,则很难完全将污染物从膜面上清洗掉,针对特定的污染,只有采取相应的清洗方法,才能达到好的效果,若错误地选择清洗化学药品和方法,有时会使膜系统污染加剧。因此在清洗之前需先决定膜表面的污垢种类,有以下几种分析方法:
分析系统性能数据,请参阅故障排除一节的详细介绍
分析进水组成,发生污垢的可能性或许经过分析原水水质报告,就能显而易见的发现
检查前几次的清洗效果
分析测定SDI值的微孔滤膜膜面上所截留的污物
分析保安滤器滤芯上的沉积物
检查进水管内表面及RO膜元件的进出水端面,如为红棕色,则表示可能已发生铁的污染;泥状或胶状沉积物通常为微生物或有机物污染。
2.清洗条件
在正常操作过程中,RO反渗透膜元件内的膜片会受到无机盐垢、微生物、胶体颗粒和不溶性的有机物质的污染。操作过程中这些污染物沉积在膜表面,导致标准化的产水流量和系统脱盐率分别下降或同时恶化。当下列情况出现时,需要清洗膜元件:
标准化产水量降低10%以上
进水和浓水之间的标准化压差上升了15%
标准化透盐率增加5%以上
以上的标准(基准)比较条件取自系统经过最初48小时运行时的操作性能。
日常操作时必须测量和记录每一段压力容器间的压差(ΔP),随着元件内进水通道被堵塞,ΔP将增加。需要注意的是,如果进水温度降低,元件产水量也会下降,这是正常现象并非膜的污染所致。预处理、压力控制失常或回收率的增加将会导致产水量的下降或透盐量的增加。当观察到系统出现问题时,此时元件可能并不需要清洗,但应该首先考虑这类原因。为了对选用RO膜元件的系统性能数据进行标准化。
膜的使用寿命取决于膜的化学稳定性、元件的物理稳定性、可清洗性、进水水源、预处理、清洗频率、操作管理水平等。国际品牌的RO反渗透膜(进口品牌的RO反渗透膜公司居多)根据经济分析通常为3年以上,进口品牌的RO反渗透膜公司的RO膜综合性价比高、稳定性好、寿命长等。如:美国菲欧姆泰克膜FILMTEC膜公司,母公司为美国杜邦膜DUPONT膜公司,美国明尼苏达州Minnesota(MN)USA,美国。美国菲欧姆泰克膜FILMTEC膜公司,母公司为美国陶氏膜DOW膜公司,美国明尼苏达州Minnesota(MN)USA,美国。美国奥斯莫尼斯膜OSMONICS膜公司,美国明尼苏达州Minnesota(MN)USA,美国。美国迪赛欧膜DESAL膜公司,母公司为美国奥斯莫尼斯OSMONICS公司,美国明尼苏达州Minnesota(MN)USA,美国。美国海德能膜HYDRANAUTICS膜公司,美国明尼苏达州Minnesota(MN)USA,美国,母公司为日本NITTO日东电工,日本公司。美国科氏膜KOCH膜公司,美国加利福尼亚州,California(CA)USA,美国。美国菲姆赛博膜FILMSEP膜公司,美国明尼苏达州Minnesota(MN)USA,美国。美国安孚膜AMFOR膜公司,美国明尼苏达州Minnesota(MN)USA,美国。德国迈纳德膜公司,德国。美国nanoh2o膜公司,美国明尼苏达州Minnesota(MN)USA,美国,母公司韩国LG chem公司,韩国。日本东洋纺TOYOBO膜公司,日本。日本ROMEMBRA膜品牌,母公司为日本东丽膜TORAY膜公司,RO膜公司的国产化公司在中国北京和广东;中国的蓝星东丽膜TBMC膜公司;韩国世韩CSM膜公司,韩国。俄罗斯MEMBRANIUM膜公司.德国朗盛膜LANXESS膜公司,德国。印度LEXCRU膜公司。等等。
3.清洗安全注意事项
在下列各章节中,当使用任何清洗化学品时,必须遵循获得认可的安全操作规程。关于化学品安全性、使用方法和排放处置方面的细节请咨询该化学品制造商。
当准备清洗液时,应确保在进入元件循环之前,所有的清洗化学品得到很好的溶解和混合。
在清洗化学药品与膜元件循环之后,应采用高品质的不含余氯等氧化剂的水对膜元件进行冲洗(最低温度>20ºC),推荐用膜系统的产水,如果对管道没有腐蚀问题时,可用经脱氯的饮用水和经预处理的给水。在恢复到正常操作压力和流量前,必须注意开始要在低流量和压力下冲洗大量的清洗液。此外,在清洗过程中清洗液也会进入产水侧,因此,产水必须排放10分钟以上或直至系统正常启动运行后产水清澈为止。
在清洗液循环期间,pH2~10时温度不应超过50ºC,pH1~11时温度不应超过35ºC,pH1~12时温度不应超过30ºC。
对于直径大于6英寸的元件,清洗液流动方向与正常运行方向必须相同,以防止元件产生“望远镜”现象,因为压力容器内的止推环仅安装在压力容器的浓水端。在小型元件的系统清洗时也建议注意这一点。清洗流程示意如下。
4.清洗设备
清洗所需设备参见下面的清洗系统流程图,针对RO膜元件的清洗液pH值范围可能在1~12之间,因此清洗系统应采用耐腐蚀材料建造。
作混合与循环的清洗水箱可以是聚丙烯或玻璃钢(FRP),清洗水箱应设有可移动的盖子和温度表计,提高清洗温度有利于提高清洗效率,在此建议清洗过程中应按表7-2的规定维持清洗液pH值和温度的恒定。由于低 温下清洗化学动力学极低,清洗液温度不应低于15ºC(59ºF),此外,某些化学品如月桂酸钠(十二烷基磺酸钠)在低温下可能发生沉淀,在某些地区,清洗系统中则需要安装冷却部件,因此设计清洗系统时应考虑加热和冷却要求。确定清洗箱大小的大致方法是将空的压力容器的体积与清洗液循环管路的体积之和,例如清洗10支含6芯的8英寸元件压力容器的系统,采用下列计算:
压力容器的体积
V1 =pr2L
=3.14(4 in)2(20ft)(7.48 gal/ft3)/144 in2/ft2)
=52 加仑/压力容器(0.20m3)
V10 =52x10=520 加仑(1.97m3)
管线的体积,假设使用50英尺长,4英寸管道
Vp =pr2L
=3.14(1.91 in)2(50ft)(7.48 gal/ft3)/144 in2/ft2)
=30 加仑(0.11m3)
Vct = V10+ Vp =520+30 =550加仑(2.08m3)
因此,所需配制的清洗液体积约为550加仑(2.08m3),由于清洗箱完全装满可能产生溢流,一般应考虑20%的裕度,本例应选择公称体积为700加仑(2.5m3)的耐腐蚀水箱作清洗箱。 根据元件型号及污染程度而定
对于一般污染情况: 每支4040型膜元件需配制8.5升清洗液;
每支8英寸膜元件需配制34升清洗液。
对于严重污染情况: 每支4040型膜元件需配制16升清洗液;
每支8英寸膜元件需配制55升清洗液。
清洗泵的大小根据表的流量和压力再加上管路和滤芯的压力损失来选择,水泵的材质至少必须是316不 锈钢或非金属聚酯复合材料。
清洗系统中应设有必要的阀门、流量计和压力表以控制清洗流量,联结管线既可以是硬管也可以是软管,清洗管道流速应小于3米/ 秒(10 英尺/ 秒)。
5.清洗步骤
5.1 清洗单段系统
采取如下六个步骤清洗膜元件:
配制清洗液
低流量输入清洗液。
首先用清洗水泵混合一遍清洗液,预热清洗液时应以低流量(表所列值的一半)。
然后以尽可能低的清洗液压力置换元件内的原水,其压力仅需达到足以补充进水至浓水的压力损失即可,即压力必须低到不会产生明显的渗透产水。低压置换操作能够最大限度的减低污垢再次沉淀到膜表面,视情况而定,排放部分浓水以防止清洗液的稀释。
表. 高流量循环期间每支压力容器建议流量和压力
1 取决于压力容器内元件数量;2 4英寸full-fit元件清洗流量为12~14gpm(2.7~3.2 m3/h);
表 清洗pH值和温度极限
循环。
当原水被置换掉后,浓水管路中就应该出现清洗液,让清洗液循环回清洗水箱并保证清洗液温度恒定。
浸泡。
停止清洗泵的运行,让膜元件完全浸泡在清洗液中。有时元件浸泡大约1小时就足够了,但对于顽固的污染物,需要延长浸泡时间,如浸泡10~15小时或浸泡过夜。为了维持浸泡过程的温度,可采用很低的循环流量(约为表所示流量的10%)。
高流量水泵循环。
按表所列的流量循环30~60分钟。高流量能冲洗掉被清洗液清洗下来的污染物。如果污染严重,请采用 高于表所规定的50%的流量将有助于清洗,在高流量条件下,将会出现过高压降的问题,单元件最大允 许的压降为1bar(15psi),对多元件压力容器最大允许压降为3.5bar(50psi),以先超出为限。
冲洗。
预处理的合格产水可以用于冲洗系统内的清洗液,除非存在腐蚀问题(例如,静止的海水将腐蚀不锈钢管道)。为了防止沉淀,最低冲洗温度为20℃。
附注 在酸洗过程中,应随时检查清洗液pH值变化,当在溶解无机盐类沉淀消耗掉酸时,如果pH的增加超过0.5 个pH值单位,就应该向清洗箱内补充酸,酸性清洗液的总循环时间不应超过20分钟,超过这一时间后,清洗液可能会被清洗下来的无机盐所饱和,而污染物就会再次沉积在膜表面,此时应用合格预处理产水将膜系统及清洗系统内的第一遍清洗液排放掉,重新配置清洗液进行第二遍酸性清洗操作。如果系统必须停机24小时以上,则应将元件保存在1%(重量比)的亚硫酸氢钠水溶液中。在对大型系统清洗之前,建议从待清洗的系统内取出一支膜元件,进行单元件清洗效果试验评估。
5.1 清洗多段系统
在多段系统的冲洗和浸泡步骤中,可以对整个系统的所有段同时进行,但是对于高流量的循环必须分段进行,以保证循环流量对第一段不会太低而对最后一段不会太高,这可以通过一台泵每次分别清洗各段或针对每段流量要求设置不同的清洗泵来实现。
6. 清洗药剂
表列举了适宜的清洗药品,这些酸性和碱性清洗剂是标准的清洗药品,酸性清洗剂用于清除包括铁污染在内 的无机污染物,而碱性清洗剂用于清洗包括微生物在内的有机污染物。由于使用硫酸会引起硫酸钙沉淀的危险,不应选作清洗剂。最好采用膜系统的产水配制清洗液,当然在很多情况下也可以使用经过预处理的合格预处理出水来配制清洗液。原水可能缓冲容量很大,需要消耗更多的酸或碱才能达到规定的pH值,酸性清洗的pH约为2左右,碱性清洗的pH约为12左右。
表RO膜元件一般清洗液
(W)表示有效成份的重量百分含量;
按顺序污染物化学式符号为:CaCO3表示碳酸钙;CaSO4表示硫酸钙;BaSO4表示硫酸钡。
按顺序清洗化学品符号为:NaOH表示氢氧化钠;Na4EDTA表示乙二胺四乙酸四;Na-SDS表示十二烷基磺酸钠盐,又名月硅酸钠;HCl表示盐酸;Na2S2O4表示亚硫酸氢钠;H3PO4 表示磷酸;NH2SO3H表示亚硫酸氢胺。
为了有效的清洗硫酸盐垢,必须尽早的发现和处理,由于硫酸盐垢的溶解度随清洗液含盐量的增加而增加,可以在NaOH和Na4EDTA的清洗液中添加NaCl,当结垢一周以上时,硫酸盐垢的清洗成功性值得怀疑。
柠檬酸是无机盐垢的可选清洗剂。
7 膜系统消毒
7.1 引 言
生物污染是RO/NF系统操作中最常见和最严重的问题之一,特别是当水源为地表水或富含细菌的进水,控制水中微生物的活动尤为重要,正确的设计和预处理操作是防止出现微生物污堵的先决条件,完整的取样和分析步骤是操作程序的一部分,这样微生物活动的增加在早期阶段就可发现。关于评估生物污堵可能性的方法请参阅“预防生物污染”一节,关于微生物取样点设置和系统检查方法请查阅微生物活动的监控一节。
7.2 清洗受生物污染的RO膜元件
下列清洗程序是专门针对受生物污染的膜系统,对于所有清洗过程,其清洗系统配置、pH和温度范围及建议清洗流量值完全相同,建议参考通用清洗导则的规定。
清洗步骤
采取七个步骤清洗受生物污染的膜元件:
按表配制清洗液。
表 生物污染清洗液
1 (wt)表示有效成份的重量百分含量;2 按顺序清洗化学品符号为:NaOH表示氢氧化钠;Na-SDS表示十二烷基苯磺酸
低流量输入清洗液。
当清洗水泵混合清洗液,清洗液预热以及用清洗液置换元件内的原水时,应按表7-5所列流量值的一半即按 低流量和低压力操作条件进行,所需的压力仅需达到足以补充进水至浓水的压力损失即可。压力必须低到不会产生明显的渗透产水。低压能够最大限度的减低污垢再次沉淀到膜表面,视情况而定,应排放部分浓水以防止清洗液的稀释。
循环。
当原水被置换掉后,浓水管路中就应该出现清洗液,可以让清洗液循环返回清洗液水箱。循环清洗液15分钟或直到颜色不变为止。如果颜色仍发生变化,放掉清洗液重新按步骤1)配置新的清洗液。
浸泡。
停止清洗泵的运行,让膜元件完全浸泡在清洗液中。元件浸泡时间1~15小时(浸泡过夜将更好)。为了维持浸泡过程的温度,可采用很低的循环流量(约为表所示流量的10%)。浸泡时间随污染严重程度而定,对于 轻度污染,浸泡1~2小时足够。
高流量水泵循环。
按表所示的流量循环45分钟。高流量能冲洗掉被清洗液清洗下来的污染物。如果污染严重,请采用高于 表所规定的50%的流量将有助于清洗,在高流量条件下,将产生过高压降的问题,单元件最大允许的压 降为1bar(15psi),对多元件压力容器最大允许压降为3.5bar(50psi),以先超出为限。
表 在高流量循环期间每支压力容器推荐流量
1. 取决于压力容器内元件数量;2. 4英寸full-fit元件清洗流量为12~14gpm(2.7~3.2 m3/h
冲洗。
经预处理的合格预处理出水可以用于冲洗清洗液,除非存在腐蚀问题(如静止的海水将会腐蚀不锈钢管道)。为了防止沉淀,最低冲洗温度为20 ℃ ,系统冲洗时间约1小时。
重新启动系统。
必须等待元件和系统达到稳定后,记录系统重新启动后的运行参数,清洗后系统性能恢复稳定的时间取决于原先污染的程度。为了获得最佳的性能,有时需要多次的清洗和浸泡步骤。
附加信息
实践表明,含Na4-EDTA的碱性清洗液清洗效果不及标准碱性溶液或含Na-SDS的碱性溶液。
对任何清洗液而言,清洗液与膜元件的接触时间最重要。为了恢复系统性能,有时需要数次清洗液浸泡过夜。在元件清洗之后,再清洗一次才可以非常有效地除去膜面上残留的生物污染膜。任何残留的生物污染膜将会吸引和捕捉污染物,所以,再清洗一遍将有利于延长清洗周期,提高系统性能。
对于工业用水而言,或产品水不是以饮用为目的时,可以在步骤1)前使用非氧化性的杀菌剂以消灭系统中的细菌和生物膜。请参阅膜系统消毒指南(即用非氧化性的DBNPA消毒)。如果只能使用氧化剂例如过氧化氢消毒,则必须先清洗后消毒。
7.3 用DBNPA消毒
膜通常易于受各种污染,其中产生微生物污染的一个原因是由于细菌活动所致。生物污染会形成富集其它腐殖质的基础条件并导致更为严重的问题,此时受污染的膜系统产水量下降,运行压力增加,脱盐率降低,当上述任一症状出现时,就应怀疑出现了微生物污染,用户应使用杀菌消毒剂,尝试“再生”RO膜系统,以下是对杀菌消毒剂的要求:
与膜兼容,
能发挥较快的消毒作用
成本较低
有易于运输,贮存和操作以及稳定的特点
不应透过膜进入产水中
有广谱杀菌作用能力
可生物降解
符合当前和未来的各种法规。
符合这些要求的杀菌消毒剂为DBNPA(2,2-dibromo-3-nitrilo-proprionamide,2,2-双溴代-3-次氮基-丙酰胺),目 前有几种含DBNPA的产品可供选用,要了解更多关于DBNPA或希望找到水处理药剂的供应商,请咨询抗菌剂。
消毒频率和步骤
RO/NF系统运行在高微生物活动的进水中时,在接触各种微生物之后的3~5天就会出生物膜,因此,在生物活动旺盛期(夏季),最常规的消毒频率为每3~5天一次,在生物活动非旺盛期(冬季),大约每7天一次,最佳的消毒频率应根据每个系统的实际情况而定,有两种消毒方法可供选择,短暂或连续加药。
当短暂加药时,使用DBNPA的量取决于微生物污染的严重程度,生物活动低的水源,每5天加入10~30ppm的活性成份30分钟到3小时处理。如果水中含100CFU/ml(菌落总数/毫升)或已经确诊为存在生物膜污染时,建议投加方式为连续3小时30ppm。由于DBNPA可以被还原剂分解(例如亚硫酸氢钠),水中含有还原剂时,需投加更高浓度的DBNPA,每1ppm残留还原剂要添加1ppm有效DBNPA。为了清除杀死的生物膜,建议使用碱性清洗剂,详见“清洗受生物污染的RO膜元件”一节的介绍,杀菌剂、杀菌剂的分解产物和杀菌剂配方中的其 它成份并不能被膜所完全脱除,因此在投加杀菌消毒剂期间,可能需要将产水排放掉不要。
一旦系统消除了严重的生物膜污染之后,必须采取连续的防范措施,建议连续投加0.5~1.0ppm的有效DBNPA,加药量可根据生物活动的程度的高低作相应调整,按照这种模式使用DBNPA,就可以在膜系统内将细菌数量控制在零含量。
虽然DBNPA是非氧化性药剂,但当其浓度<0.5ppm或>3ppm时,它会在ORP上大约会有+400mV的响应值,而每1ppm的氧化性氯和溴在ORP上的响应值是+700mV,还会随浓度增加而增加响应值。
7.4 用过氧化氢杀菌与消毒
装有RO膜元件的系统可以成功地使用过氧化氢或过氧化氢与过乙酸的混合物进行杀菌与消毒。有些产品是浓缩产品,使用前用膜系统产水按1:100比例稀释,得到0.25%过氧化物稀溶液。
但一般有两个因素,温度和铁,会引起过氧化氢对膜的攻击损伤,杀菌溶液不应超过25℃,以0.5%过氧化氢在34℃时对膜样品作试验发现,数小时之后,样品膜的透盐率就相当高了,但同样浓度当温度在24℃时,经过96小时接触,膜性能仍不受影响。
有铁或其它过渡金属的存在时,过氧化氢也会引起膜的降解,膜样品在0.15%过氧化氢和含铁的自来水试验150小时之后,膜的透盐率显著地增加了。
当使用过氧化氢杀菌时,建议清洗杀菌步骤如下:
在杀菌之前,膜面或系统其它部件任何形式的沉淀必须用碱性清洗液清除掉,清除掉这些蕴藏微生物的沉积物可以提高杀菌消毒效果,碱性清洗之后,再用膜系统的产水冲洗系统。
酸洗膜系统,如用0.1%HCl或0.4%磷酸,从膜表面除铁,再用膜系统的产水冲洗系统。
控制温度25℃以下,以0.2%过氧化氢溶液,循环20分钟,用HCl调节pH3~4以获得最好的杀菌效果和更长的膜寿命。
将膜元件浸泡在杀菌液中2~12小时,浸泡2小时可以将90%的细菌杀死,而12小时浸泡可以杀死99%的细菌。
用膜系统的产水冲洗整个系统。
7.5 含氯杀菌消毒剂
以下的建议适用膜微生物防护和消毒灭菌,在使用以下各节所述化学品时,请遵循安全操作规范,有关化学品安全、处理和丢弃方面的详细问题,请咨询相应化学品供应商。
膜保存
在贮存,运输或系统停运期间,为了防止微生物的生长,我们建议将RO膜元件浸泡在保护液中,标准保护液含1%(wt)食品级亚硫酸氢钠,这种保护液不应对膜通量或其它性能产生不利的影响。
含氯杀菌剂
RO膜可以承受短期的游离氯(次氯酸)的接触,但是对它的抵抗能力是有限的;膜元件可以在出现短暂性接触自由氯的系统里仍有良好的运行性能表现,大约与1ppm自由氯接触200~1000小时之后,会发生实质性的降解。氯的攻击速率取决于进水的各种条件,在碱性pH条件下氯的攻击速度要高于在中性或酸性的pH条件,在含重金属(如铁)的条件下,氯的攻击速度也会加快,因为重金属能催化这一降解反应,因此不建议采用含氯的杀菌消毒剂,这类杀菌剂包括氯胺,氯胺-T和N-氯异氰酸酯(N-chlorois℃yanurate),在低浓度下,膜对这类温 和的含氯药剂有抵抗力,然而,在低浓度范围内,作为消毒剂其杀菌效能很有限,同时,这些化合物也会缓慢地破坏膜,因为它与少量的余氯存在平衡。
如果贮存期小于1周,可以有效地使用浓度为500ppm的高纯度ClO2作杀菌消毒剂。但是它不能作为更长贮存期使用的有效杀菌剂,在使用现场由氯气和氯化钠反应就地制备的ClO2中总会含有余氯,这样膜元件就会受到含余氯的ClO2攻击,氯胺和ClO2可以透过RO膜片,在产水中残留少量的杀菌剂。
7.6 其它杀菌剂
允许过氧化氢和过乙酸的最高浓度为0.2%,最高温度为25℃,否则会破坏膜,同时还不得存在等重金属,因为它们会对膜降解过程起到催化作用。连续性地让膜接触以上的浓度,最终也会出现膜的损坏,因此,建议间歇性地使用它。
甲醛必须在膜元件连续运行至少6小时之后,才可以使用,否则会出现产水量的衰减,经过这一连续初始运行之后,可以使用0.5%~3%的甲醛进行系统杀菌及长期停用保护。但研究表明,甲醛具有致癌倾向,被逐渐限制使用。
硫酸铜可以用来控制藻类的滋生,通常硫酸铜连续投加量为0.1~0.5ppm,同时pH必须足够地低,以防止氢氧化铜的沉淀。碘、四价杀菌剂和酚类化合物会引起膜通量的下降,不能作为杀菌消毒剂。
8 特定污染物的清洗
8.1 清洗硫酸盐垢
下列清洗程序是专门针对硫酸盐垢污染的系统,硫酸盐垢的污染是非常难以清洗的一类膜污染物,如果硫酸盐类垢不能在早期发现,膜系统性能能够清洗恢复的可能性极低,最有可能是将出现产水量的下降并难以恢复。对产生硫酸盐垢一周以上时,试图用清洗的方法恢复系统性能往往是不经济的,而更换元件可能是更好的选择。对于所有清洗过程,其清洗系统配置、pH和温度范围及建议清洗流量值完全相同,建议参考通用清洗导则的规定。
清洗步骤
采取七个步骤清洗硫酸盐垢污染的膜元件:
按表配制清洗液:
编辑
1 (wt)表示有效成份的重量百分含量;
2 按顺序清洗化学品符号为:NaOH表示氢氧化钠;Na4-EDTA表示乙二胺四乙酸四钠。
3 为了硫酸盐结垢的有效清洗,应尽早抓住和处理发生硫酸盐结垢的条件。由于硫酸盐的溶解度会随溶液含盐量的增加而增加,在 NaOH和Na4-EDTA的清洗溶液中加入NaCl可能对清洗有所帮助。硫酸盐结垢一周以上,清洗硫酸盐结垢的成功可能性值得怀疑。
低流量输入清洗液。
当清洗水泵混合清洗液,清洗液预热以及用清洗液置换元件内的原水时,应按表所列流量值的一半即按 低流量和低压力操作条件进行,所需的压力仅需达到足以补充进水至浓水的压力损失即可。压力必须低到不会产生明显的渗透产水。低压能够最大限度的减低污垢再次沉淀到膜表面,视情况而定,应排放部分浓水以防止清洗液的稀释。
循环。
当原水被置换掉后,浓水管路中就应该出现清洗液,可以让清洗液循环返回清洗液水箱。循环清洗液约30分钟。
浸泡。
停止清洗泵的运行,让膜元件完全浸泡在清洗液中。元件浸泡时间1~15小时(浸泡过夜将更好)。为了维持浸泡过程的温度,可采用很低的循环流量(约为表所示流量的10%),浸泡时间随污染严重程度而定。
高流量水泵循环。
按表所列的流量循环30分钟。高流量能冲洗掉被清洗液清洗下来的污染物。如果污染严重,请采用高于 表所规定的50%的流量将有助于清洗,在高流量条件下,将产生过高压降的问题,单元件最大允许的压 降为1bar(15psi),对多元件压力容器最大允许压降为3.5bar(50psi),以先超出为限。
冲洗。
经预处理的合格预处理出水可以用于冲洗清洗液,除非存在腐蚀问题(如静止的海水将会腐蚀不锈钢管道)。为了防止沉淀,最低冲洗温度为20℃,系统冲洗时间约1小时。
重新启动系统。
必须等待元件和系统达到稳定后,记录系统重新启动后的运行参数,清洗后系统性能恢复稳定的时间取决于原先污染的程度。为了获得最佳的性能,有时需要多次的清洗和浸泡步骤。但是对硫酸盐结垢而言,预计会有永久性的通量损失。
8.2 清洗碳酸盐垢
下列清洗程序是专门针对存在碳酸盐垢沉淀膜系统的清洗,对于所有清洗过程,其清洗系统配置、pH和温度范围及建议清洗流量值完全相同,建议参考通用清洗导则的规定。
清洗步骤
采取七个步骤清洗存在碳酸盐垢沉淀的膜元件:
按表配制清洗液:
表 碳酸盐垢清洗液
1 (wt)表示有效成份的重量百分含量;2 按顺序清洗化学品符号为:HCl表示盐酸;Na2S2O4表示连二亚硫酸钠(亚硫
低流量输入清洗液。
当清洗水泵混合清洗液,清洗液预热以及用清洗液置换元件内的原水时,应按表所列流量值的一半即按 低流量和低压力操作条件进行,所需的压力仅需达到足以补充进水至浓水的压力损失即可。压力必须低到不会产生明显的渗透产水。低压能够最大限度的减低污垢再次沉淀到膜表面,视情况而定,应排放部分浓水以防止清洗液的稀释。
循环。
当原水被置换掉后,浓水管路中就应该出现清洗液,可以让清洗液循环返回清洗液水箱。循环清洗液10分钟或直到颜色不变为止。如果任何循环过程中存在pH的变化和清洗液颜色的变化,放掉清洗液重新按步骤1)配置新的清洗液,在清洗过程中应保持pH2以便实现有效的清洗。
浸泡。
停止清洗泵的运行,让膜元件完全浸泡在清洗液中。元件浸泡时间1~15小时(浸泡过夜将更好)。为了维持浸泡过程的温度,可采用很低的循环流量(约为表所示流量的10%),浸泡时间随污染严重程度而定,对 轻度污染,浸泡1~2小时足够。
高流量水泵循环。
按表所列的流量循环10分钟。高流量能冲洗掉被清洗液清洗下来的污染物。如果污染严重,请采用高于 表所规定的50%的流量将有助于清洗,在高流量条件下,将产生过高压降的问题,单元件最大允许的压 降为1bar(15psi),对多元件压力容器最大允许压降为3.5bar(50psi),以先超出为限。
冲洗。
经预处理的合格预处理出水可以用于冲洗清洗液,除非存在腐蚀问题(如静止的海水将会腐蚀不锈钢管道)。为了防止沉淀,最低冲洗温度为20℃,系统冲洗时间约1小时。
重新启动系统。
必须等待元件和系统达到稳定后,记录系统重新启动后的运行参数,清洗后系统性能恢复稳定的时间取决于原先污染的程度。为了获得最佳的性能,有时需要多次的清洗和浸泡步骤。
附加信息
清洗液循环不得超过20分钟,因为长时间的循环,碳酸盐将再次沉淀并堵住元件的末端,使得清洗更加困难,清洗过程中,碳酸盐垢与盐酸的反应会释放二氧化碳。取决于污染的严重程度,或许需要重复清洗以除去所有的结垢。清洗严重的结垢可能并不经济,而此时元件更换可能是更好的选择。
以柠檬酸为有效成份的酸性清洗配方原来是为清洗醋酸纤维素类膜元件设计的,实践证明用于聚酰胺类复合膜的化学清洗并不有效,而且清洗费昂贵。更为特别的是,它有成为系统内微生物养分的缺点,引起生物污染。然而其挥发性低,就操作安全性而言比盐酸使用方便,因为这一原因,将其列为可选清洗剂。
8.3 清洗铁污染
下列清洗程序是专门针对存在铁污染膜系统的清洗,对于所有清洗过程,其清洗系统配置、pH和温度范围及建议清洗流量值完全相同,建议参考通用清洗导则的规定。
采取七个步骤清洗存在铁污染的膜元件:
按表配制清洗液:
表 铁污染清洗液
1 (wt)表示有效成份的重量百分含量;
2 按顺序清洗化学品符号为:Na2S2O4表示连二亚硫酸钠(亚硫酸氢钠);H3PO4表示磷酸;NH2SO3H表示亚硫酸氨。
低流量输入清洗液。
当清洗水泵混合清洗液,清洗液预热以及用清洗液置换元件内的原水时,应按表所列流量值的一半即按 低流量和低压力操作条件进行,所需的压力仅需达到足以补充进水至浓水的压力损失即可。压力必须低到不会产生明显的渗透产水。低压能够最大限度的减低污垢再次沉淀到膜表面,视情况而定,应排放部分浓水以防止清洗液的稀释。
循环。
当原水被置换掉后,浓水管路中就应该出现清洗液,可以让清洗液循环返回清洗液水箱。循环清洗液15钟或直到颜色不变为止。如果任何循环过程中存在pH的变化和清洗液颜色的变化,放掉清洗液重新按步骤1)配置新的清洗液。
浸泡。
停止清洗泵的运行,让膜元件完全浸泡在清洗液中。元件浸泡时间1~15小时(浸泡过夜将更好)。为了维持浸泡过程的温度,可采用很低的循环流量(约为表所示流量的10%),浸泡时间随污染严重程度而定,对 轻度污染,浸泡1~2小时足够。
高流量水泵循环。
按表所列的流量循环45分钟。高流量能冲洗掉被清洗液清洗下来的污染物。如果污染严重,请采用高于 表所规定的50%的流量将有助于清洗,在高流量条件下,将产生过高压降的问题,单元件最大允许的压 降为1bar(15psi),对多元件压力容器最大允许压降为3.5bar(50psi),以先超出为限。
冲洗。
经预处理的合格预处理出水可以用于冲洗清洗液,除非存在腐蚀问题(如静止的海水将会腐蚀不锈钢管道)。为了防止沉淀,最低冲洗温度为20℃,系统冲洗时间约1小时。
重新启动系统。
必须等待元件和系统达到稳定后,记录系统重新启动后的运行参数,清洗后系统性能恢复稳定的时间取决于原先污染的程度。为了获得最佳的性能,有时需要多次的清洗和浸泡步骤。
附加信息
连二亚硫酸钠具有非常刺激性的气味,清洗间必须通风良好,必须遵循所有的安全操作规定和程序。
接触时间是成功达到清洗目的关键所在。有时清洗液会变成很多不同的颜色,对这类清洗,黑色、棕色、黄色均属正常。任何时候,清洗液颜色发生变化时,该清洗液应排放掉,并配置新的清洗液,浸泡的时间长短和次数取决于污染的严重性。
以柠檬酸为有效成份的酸性清洗配方原来是为清洗醋酸纤维素类膜元件设计的,实践证明用于聚酰胺类复合膜的化学清洗并不有效,而且清洗费昂贵。更为特别的是,它有成为系统内微生物养分的缺点,引起生物污染。然而其挥发性低,就操作安全性而言比连二亚硫酸钠(亚硫酸氢钠)使用方便,因为这一原因,将其列为可选清洗剂。
8.4 清洗有机物污染
下列清洗程序是专门针对存在有机物如腐植酸和富里酸、阻垢剂或油等污染膜系统的清洗,对于所有清洗过程,其清洗系统配置、pH和温度范围及建议清洗流量值完全相同,建议参考通用清洗导则的规定。
采取六个步骤清洗存在有机物污染的膜元件,但这六个清洗步骤需要重复进行,一次为高pH清洗液,另一次为低pH清洗液:
按表配制清洗液:
表 有机物污染清洗液
清洗液
1 (wt)表示有效成份的重量百分含量;
2 按顺序清洗化学品符号为:NaOH表示氢氧化钠;Na-SDS表示十二烷基苯磺酸钠;Na4-EDTA表示乙二胺四乙酸四钠。
低流量输入清洗液。
当清洗水泵混合清洗液,清洗液预热以及用清洗液置换元件内的原水时,应按表所列流量值的一半即按 低流量和低压力操作条件进行,所需的压力仅需达到足以补充进水至浓水的压力损失即可。压力必须低到不会产生明显的渗透产水。低压能够最大限度的减低污垢再次沉淀到膜表面,视情况而定,应排放部分浓水以防止清洗液的稀释。
循环。
当原水被置换掉后,浓水管路中就应该出现清洗液,可以让清洗液循环返回清洗液水箱,循环清洗液30分钟如果清洗液颜色仍发生变化,放掉清洗液重新按步骤1)配制新的清洗液。
浸泡。
停止清洗泵的运行,让膜元件完全浸泡在清洗液中。元件浸泡时间1~15小时(浸泡过夜将更好)。为了维持浸泡过程的温度,可采用很低的循环流量(约为表所示流量的10%),浸泡时间随污染严重程度而定,对 轻度污染,浸泡1~2小时足够。
高流量水泵循环。
按表所列的流量循环30分钟。高流量能冲洗掉被清洗液清洗下来的污染物。如果污染严重,请采用高于 表所规定的50%的流量将有助于清洗,在高流量条件下,将产生过高压降的问题,单元件最大允许的压 降为1bar(15psi),对多元件压力容器最大允许压降为3.5bar(50psi),以先超出为限。
冲洗。
经预处理的合格预处理出水可以用于冲洗清洗液,除非存在腐蚀问题(如静止的海水将会腐蚀不锈钢管道)。为了防止沉淀,最低冲洗温度为20℃,系统冲洗时间约1小时。
用pH为2的HCl溶液重复步骤2)至6)。
重新启动系统。
必须等待元件和系统达到稳定后,记录系统重新启动后的运行参数,清洗后系统性能恢复稳定的时间取决于原先污染的程度。为了获得最佳的性能,有时需要多次的清洗和浸泡步骤。
附加信息
为了最大地提高清洗效率,清洗液的温度必须高于25℃,升高温度有利于帮助清洗液从膜面上除去有机污染物。
有些有机物如油类非常难以清洗,为了除去它们,需试验各种清洗浸泡时间以获得最佳效率。此外,最有效的清洗液通常含有表面活性剂如Na-SDS或某些商品清洗剂含有表面活性剂及洗涤剂,它们能帮助除去油污染。请咨询该化学品供应商。
如果有机污染源于预处理部分加入了过量絮凝剂,相反次序使用清洗剂(先用酸性清洗液后用碱性清洗液)更有效,为了确定合适的清洗液顺序(先高pH后低pH或反之),请设法获取系统污染物样品,针对样品先用碱性后用酸性溶液或反之,定性地确认何种顺序更好。如果效果相当,通常先用高pH清洗液清洗有机物更为合适。
8.5 紧急清洗
如果没有及时进行清洗操作,使得系统压差∆P增加了两倍,标准化产水量下降了50%,采用前面所介绍的清洗方法恢复系统性能可能会很有限,如果上述标准清洗技术难以除去污染物,就必须尝试更严劣的清洗。
在这种情况下,请与你附近的进口品牌的RO膜公司代表联络,但是必须强调地是,经这类非常规清洗之后,无法保证应有的清洗效率或膜元件的性能。
流量元件清洗液系统膜元件发布于:北京市声明:该文观点仅代表作者本人,搜狐号系信息发布平台,搜狐仅提供信息存储空间服务。Powered by 炒股按月配资网_配资炒股申请_炒股配资平台咨询 @2013-2022 RSS地图 HTML地图